SMARTER FACTORIES WITH DIGITAL TWIN
Smarter Factories with Digital Twin
The global spread of the COVID-19 coronavirus has had a large impact on how we all live and work.Many are operating again as they search for ways to operate within COVID-19 restrictions. For manufacturing sites, this means abiding by social distancing rules. It is apparent that this will require sites to operate with as few staff as possible.
We anticipate a high level of interest in automation of customer sites being driven by this situation.
This article features FUJI Smart Factory automation and digitization to attain digital twin with a focus on enabling production in which there is no difference (zero gaps) between the "virtual" and the "real".
Realizing zero gaps between the "virtual" and the "real" Configuration proposals using simulation
Two issues that arise from the advancement of automation in production sites are identifying which bottleneck processes to automate, and what automation equipment to purchase. To avoid the risk of any equipment purchased only making a minimal contribution to improvement it is important to check the effectiveness in advance, and this is where using simulation technology is effective.Such simulations involve replicating the current SMT floor in a virtual space. By taking personnel workloads, something that is hard to quantify in "real" terms, into consideration, it becomes possible to visualize bottlenecks on the SMT floor. It also becomes possible to visualize the effects from changes to operation and the introduction of automation equipment.
It is possible to specify parameters for each process including the quantities of AGVs and automatic part warehouses, the number of staff, and the designated work paths for SMT floors modeled in a virtual space to assess expected results of introducing improvement measures.
The accuracy of the data used is vital to achieving an accurate simulation. Our Integrated Production System - Nexim provides finely detailed performance results data and accurate cycle time calculations for each production type and operation method, making it an effective tool for improving the accuracy of simulations.
Scheduling the SMT floor
Production schedules are created for daily production plans by taking into account staff shifts, production order, and line allocation at production sites.However, as factories proceed with automation, more automation equipment is added to the floor, making scheduling more difficult.
By modeling the present lines and automation equipment, personnel skills, and work shifts based on the production scheduler, it is possible allocate tasks to lines and create setups that take
production order into account. Also, Nexim can calculate accurate production times where there are differences in tact time for each product type to be manufactured. By linking Nexim with the production scheduler, scheduling that includes everything from part checkout to offline changeover and the point of transportation becomes possible. (Image 1)
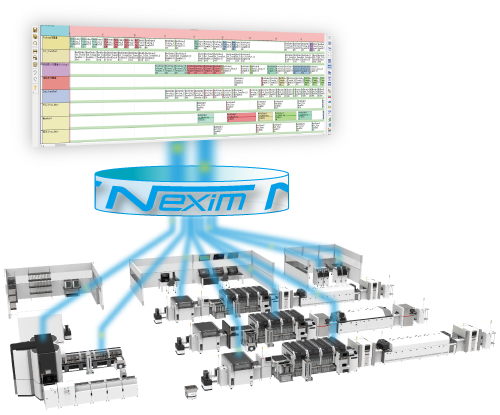
Image 1: Scheduling
Smart Factory "Monozukuri" made possible with NXTR
Issues concerning SMT lines
In current SMT placement processes, there is still a need to employ a large number of people for performing changeover and part supply work. This can cause gaps between the “real” performance and the “virtual” production schedules as different operators have different levels of skill and operate under varying conditions.For example, if multiple parts run out at the same time in a parts out rush, parts cannot be supplied in time and production is stopped. In this case, one of the reasons given is that looking for and collecting feeders and reels from part shelving for next production preparation took longer than expected.
Resolving issues at SMT lines with NXTR
Work related to parts accounts for the SMT placement processes that require the most attention from operators, and it is the problems arose here that need to be remedied., and thus it is the issues surrounding part related work processes that need to be remedied.To help improve these processes Fuji has developed the NXTR, equipped with the "Smart Loader", the world's first unit for transporting, exchanging, and setting feeders automatically at the machine. This enables automation of part exhange and supply work.
On NXTR lines, by simply setting feeders at buffer stations, the Smart Loader exchanges with the feeders in production automatically according to parts out warnings and the changeover schedule.
Regarding parts out rushes, a feeder for resupply can be set in an empty slot ready for use when the feeder currently in production runs out of parts, at which point parts will be then picked up from this "alternate supply device". After that, the empty feeder is returned, and that alternate feeder is set in the original slot. This allows for some leeway in the timing at which parts need to be supplied, making it possible to avoid parts out rushes, which in turn prevents stops in production caused by part supply issues, and production can proceed as planned.
It is possible to prepare the feeders to be used in next production and store them in the base buffer at the bottom of each module. The feeders are then set to the feeder slots in the module when required by the machine. It is possible have the feeders for next production present at the machine while performing current production, reducing the work involved at changeover. This also leads to a reduction of space the being taken up by feeder stands and carts. (Image 2) module. The feeders are then set to the feeder slots in the module when required by the machine. It is possible have the feeders for next production present at the machine while performing current production, reducing the work involved at changeover. This also leads to a reduction of space the being taken up by feeder stands and carts. (Image 2)
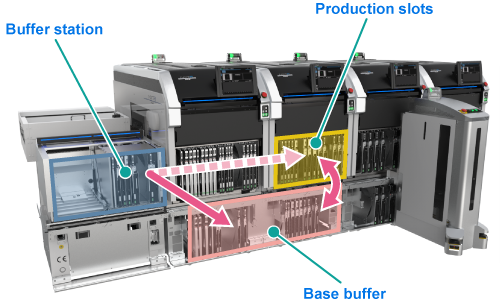
Printer evolution in all directions - NXTR PM
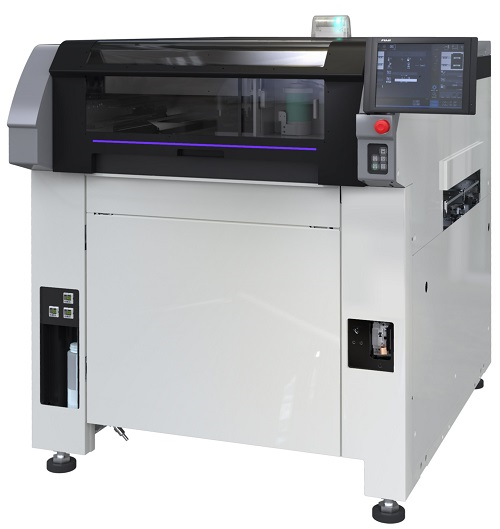
Keeping high QCD through automation
Calls to automate printing processes are increasing. We believe that this is largely due to the transformations taking place at factories in line with progress made in digital transformation (DX).The following are answers to the calls for printer automation.
Automation of material transport
Automatic transfer of automatically transported materials (masks, backup blocks)Automatic loading to the printer
Automating changeover
Automatic program changeoverAutomatic exchange of backup blocks and masks
Automatic transfer of solder onto the mask for next production and automatic supply of additional solder
Automating material supply
Exchange of empty solder cups and cleaning paper without stopping productionTo to this in a timely manner without any excess or deficiencies, it is necessary to link the production scheduler, AGVs, and pick and place machines to the printer, in this case the NXTR PM.
In terms of quality, we are strengthening cooperation with SPI machines. SPI measurement data is linked together with print parameters and perpetually stored inside the machine to build knowledge data. When creating programs, determining printing parameters is supported by using knowledge data based on the material information while checking the print quality (solder shape, height) and cycle time shown on the printer operation panel. Fuji’s printing system also reduces line stops by constantly monitoring the SPI measurement data during production, to detect trends that show the occurrence of smearing and perform cleaning before errors can occur.
Customer value service and digital twin
Supporting digital twin
As IoT technologies become more commonplace, we are seeing advancements in connected factories in which production equipment is also always connected to a network. Through this, customers will be able to collect the information needed faster when requesting support and with more accuracy. Fuji's customer value (CV) service utilizes these kinds of environments to support the feedback between "real" and "virtual" processes, which is part of digital twin.Improving productivity is a lifeline for businesses. This service covers the steps from diagnosis, analysis, investigation, proposal making, and final resolution for improving production processes. Production sites, equipment, and the service provided by Fuji, these three components are considered together for approaching issues, getting the best out of equipment and staff, and advancing production sites for contributing to higher productivity.
Visualization using diagnosis "health charts"
After production processes have been diagnosed, the resulting diagnoses are cumulated into a "health chart" to visualize whether the 5 M's (men, machines, methods, materials, and management) are in top shape, and for managing set targets, in order to visualize issues and changes in production. This chart is then shared with the customer. With this benchmark data set, a CV service covers a process of cause analysis, improvement proposals, improvement implementation, training, and result evaluation that leads to resolution of issues. Periodically undergoing this kind of diagnosis is vital to having a factory that maintains high productivity rates.
Remote diagnosis
A remote CV service can be offered when support would otherwise be difficult or when there is a request from a remote location. (Image 3)Remote diagnosis is one method for improving work styles by utilizing IoT technologies and digitalization. It serves the purpose of helping customers to create new value at their production sites with the help of Fuji.
Image 3: Remote diagnosis
The same quality service and timely response for all
With the establishment of the CV platform “CVPF”, to determine and remedy the causes of drops in productivity and quality, CV services can be provided at the same speed and quality to anywhere in the world.
With CVPF as a foundation, we are becoming more capable of providing our service in a timely manner and are working to reduce turnaround times from the analysis of "real" production sites, that is a part of digital twin solutions, to the resolution of issues.
Summary
FUJI Smart Factory has proceeded one step further with the addition of the NXTR and NXTR PM, which were developed with an emphasis on automation.NXTR, NXTR PM, and the automation of part preparation are effective tools in the effort to digitalize the actual results from "real" production sites. Additionally, the CV service improves the accuracy of feedback to "virtual" simulations by identifying problems and their causes through analysis of the gaps between production plans and actual production. CV service plays an important role to lead to better virtual outcomes by supporting the "real".
Fuji continues to support improvements at production sites by working toward enabling production that flexibly supports changes brought about by digital transformation and increased use of digital twin technology, while strengthening the automation and efficiency of work performed by machines and systems.