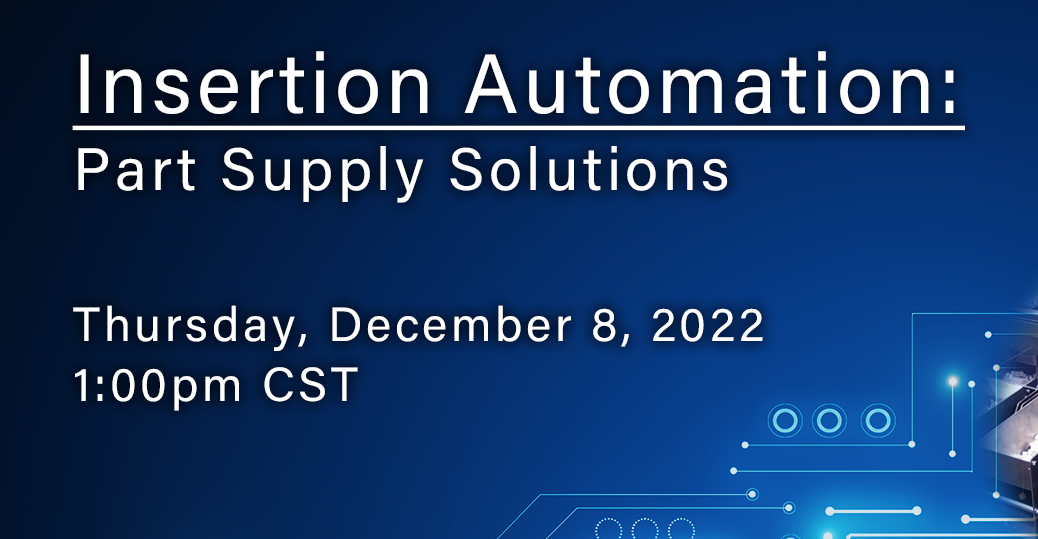
Fuji Webinar 2022 - Insertion Automation: Part Supply Solutions
Fuji is pleased to be hosting yet another webinar to discuss Insertion Automation.
Fuji is pleased to be hosting yet another webinar to discuss Insertion Automation.
We are pleased to announce that Fuji America will be holding an online webinar event to discuss another important topic: Optimizing Factory Processes.
We are pleased to announce that Fuji America will be holding an online webinar event to discuss an important topic: Automating the Insertion Process.
Do you have the following issues?
When creating production programs on placement machines, approximately 80% (Note 1) of the work is related to creating vision processing data. Creating data for package parts with multiple leads and bumps is a very difficult and time-consuming task. If vision processing data is not properly set, it can cause losses such as misalignment and machine stoppage due to part recognition errors, so this work is extremely important for ensuring quality.
Management of nozzles is vital for placement quality control, as they directly contact electrical parts. With increased product variations due to diversified customers' needs, the manufacturing industry is accelerating customization. This has resulted in an increase in the quantity and types of nozzles used for part handling. On top of that, the recent trend of miniaturization of electrical parts requires more time and effort to handle and maintain nozzles.
5G operations are now in full swing all around the world, and production of 5G base stations is proceeding at a rapid pace. Stability and improvements in processing capability are sought from 5G base stations and servers so that large data loads can be processed without delay. The electronic panels and electronic parts used in data processing are becoming larger and heavier in order to support the high-speed processing of large volumes of data and higher performance, and the SMT process must be able to respond to these changes. Here we will introduce placement solutions that are necessary for the production of 5G base station and server boards.
As market needs diversify, manufacturing sites are required to realize mass customization that realizes QCD at the same level as mass production. However, in the field of multi-product production, which frequently changes models, the decrease in production efficiency due to the increase in the number of setup changes is a major issue.
Performing changeover work offline using the "external changeover" method for the next production while the current production is being performed is an effective way to minimize the length of time production is stopped because of changeover. The Smart Setup Station is a unit specifically designed for performing this offline changeover work efficiently. By using a Smart Setup Station, operators can perform the required offline changeover work accurately without hesitation.
There is continued demand for the electronic devices we use, such as smartphones and wearable devices, to keep getting smaller while sustaining higher functionality. Also, with the proliferation of the Internet of Things we have reached the point in which communication modules and sensors are now commonplace in our home appliances and cars. This in turn has led to growth in demand for system in package (SiP) and other module parts. A common theme in the production processes for SiP and other module parts is the intertwining of cutting-edge placement technologies such as those for higher density placements, thinner structures, and multilayering.
Compared to the previous M3 III model, the throughput shows an increase of 17%. This model produced a 7% increase even when compared with the high-speed module (M3 IIIS). Fuji's technologies toward a higher rigidity for the machine body and a lighter weight sliding structure sustain a higher productivity without adverse effects on the placement accuracy.
sFAB-D machines have continued to evolve since their release to the market. They are able to insert parts into various panels with a wide range of support in part packaging. As an entry model, sFAB-SH machines are now added into the same product lineup.
There are times when an operator may set the wrong part type or set parts in the incorrect supply direction when supplying parts to the machine.
For example, when setting trays to a tray drawer there can be cases in which the incorrect parts are set or the supply direction may be wrong such as when a tray is set in the wrong direction or if someone has returned parts that have come out back into the tray by hand.
With the arrival of 5G compatible devices, there is an increased need for high-density boards like those used in high-end smartphones. 5G compatible devices require space for a greater quantity of components, and increased battery capacity. This leads to a requirement for the main board to be even more compact. Interposers are being employed as a new method for achieving high density placement. These interposers are sandwiched between two main boards for a two-tiered board.
The global spread of the COVID-19 coronavirus has had a large impact on how we all live and work. Many are operating again as they search for ways to operate within COVID-19 restrictions. For manufacturing sites, this means abiding by social distancing rules. It is apparent that this will require sites to operate with as few staff as possible. We anticipate a high level of interest in automation of customer sites being driven by this situation. This article features FUJI Smart Factory automation and digitization to attain digital twin with a focus on enabling production in which there is no difference (zero gaps) between the "virtual" and the "real".
Flexible printed circuits (FPC) are very thin with properties that allow them to be bent to a desired angle for use in electronics with movable parts and interfolded structures, and in three-dimensional wiring in devices with small interior spaces such as smartphones and wearables.
The DynaHead automatically changes tools based on the part size and shape during production. A single DynaHead can support a part range from 0402 (01005") up to 102 x 102 mm by exchanging between the R12 tool (12 nozzle operation) for smaller, chip-shaped parts, R4 tool (4 nozzle operation) for medium sized parts, and S1 (single nozzle operation) for larger, odd-form parts. Introducing a glue tool to the tool lineup also enables the DynaHead to change to a tool for dispensing glue. This glue tool can be used to provisionally secure key parts and prevent defects that occur during reflow in the form of raised parts without needing glue application independent from the placement machine. This makes it possible to both place parts with a wide range of part sizes and apply glue using the same head, which also means that a single module can become all-in-one glue and placement station.
sFAB-D, the multi-purpose automated fabrication machine, is popular product for users who want to automate insertion processes for odd-form parts.
Fuji's wealth of knowledge in the SMT industry puts Fuji in a position to be able to provide an advisory service for improvements in production.
In order to minimize the gap between the plan and reality while maintaining efficient production, optimum production schedules that include the flow of materials need to be implemented and met in actual production. FUJI Smart Factory Platform NXTR is a new platform that is able to link with the integrated production system, Nexim, for efficiently performing a wide range of production.
As electronics become smaller with greater functionality and along with demand driving shorter development times, there is an increased demand for package parts such as SiP and module parts. There are many different configurations of package parts that can be found in the market, but the common threads in the manufacturing process of these parts; multi-layering and thinner structures in the Z direction, and higher density in the XY direction, are being used in combination and continue to evolve. For these kinds of cutting-edge processes, Fuji is on hand to talk directly with factories to talk shop and provide an array of solutions.
There are a lot of settings that must be specified to create vision processing data for placement machines, and creating the data for each part to be vision processed takes time and experience. Creating vision processing data becomes especially difficult when there are elements outside the part body such as the bumps and leads on package parts. These programming issues can be remedied using Fuji's Auto Shape Generator and VPDplus.
When producing test panels or running production for very small lots, production sometimes uses parts packaged in tape that is cut in a shorter length ("shorter tape") for providing only the necessary amount of parts. This type of tape supply cannot be automated using usual tape feeders designed for mass production, so extra work such as repacking parts is required at the production floor.
Many of our customers are already using 3D coplanarity checks to check for parts with bent leads before they can result in placement defects. However, while the 3D coplanarity check unit is an accurate and versatile tool for detecting potential defects, there are also many who could benefit from the function to check for bent leads but have passed on it when weighing up the merits vs the initial costs of a unit that has a full-range capacity to check for missing or misshapen bumps, as well as missing and warped leads.
Up until now Fuji has developed and delivered many different tray part supply units that meet various needs, such as the tray unit-LT, and the stacked tray feeder. However, because electronics have such a short life cycle, the quantity and ratio of parts used changes frequently with changes in the product type. In these situations, we need to respond quickly to new challenges such as the following. • When proportionately more reel parts need to be used, and there is not enough space remaining to load a tray unit at a part supply stage. • When proportionately more tray parts need to be used, and not all parts can be loaded into the tray unit. • When only a few tray parts are used, and it might be better if there was an option that did not require an investment in a large tray unit. In answer to these kinds of issues, Fuji has developed the new "inner tray stage".
The AIMEX III is an all-in-on machine with scalability and the ultimate level of versatility necessary for increasing productivity for high-mix production. It features functions for performing operation smoothly in a short time for the work that comes with introducing new production and changing the product models to produce. The machine flexibly supports various production for users in a variety of sectors including EMS, automotive industry, and more.
In recent years we have not only seen the smartification of our computers and smart phones, but the devices that surround us as well. And we are seeing more and more of these devices connect to one another across the Internet of Things. As the much anticipated 5G network comes into our communities, the types of parts used to enable 5G technology such as communication module parts are becoming even more prevalent. As parts continue to become even smaller, thinner, and lighter, and electronic circuits are designed to be even closer together with multiple layers, electronic panels are becoming more complex than before. While these products are becoming more complex, how to maintain the same level of quality is an issue. This issue must be tackled from many angles, because while improving functionality and accuracy of equipment is important, the way materials are managed and how maintenance is performed are also contributing factors. This article will cover three areas that are important to improving quality in SMT processes and maintaining a high level of QCD, "Sure-fire pickup and placement", "Eliminating defective materials", and "Proper maintenance" with supporting data.
Depending on the operation environment, if a printer is paused for an extended period of time during production a lower volume of solder is transferred, leading to poor quality printing that results in defective products. The most common reason is that the flux present in the apertures of the screen mask dries out. Flux acts as a lubricant against the mask when solder is being filled or during snap-off. But this lubricating effect does not happen when the flux becomes dried, causing poor solder filling and poor solder release.